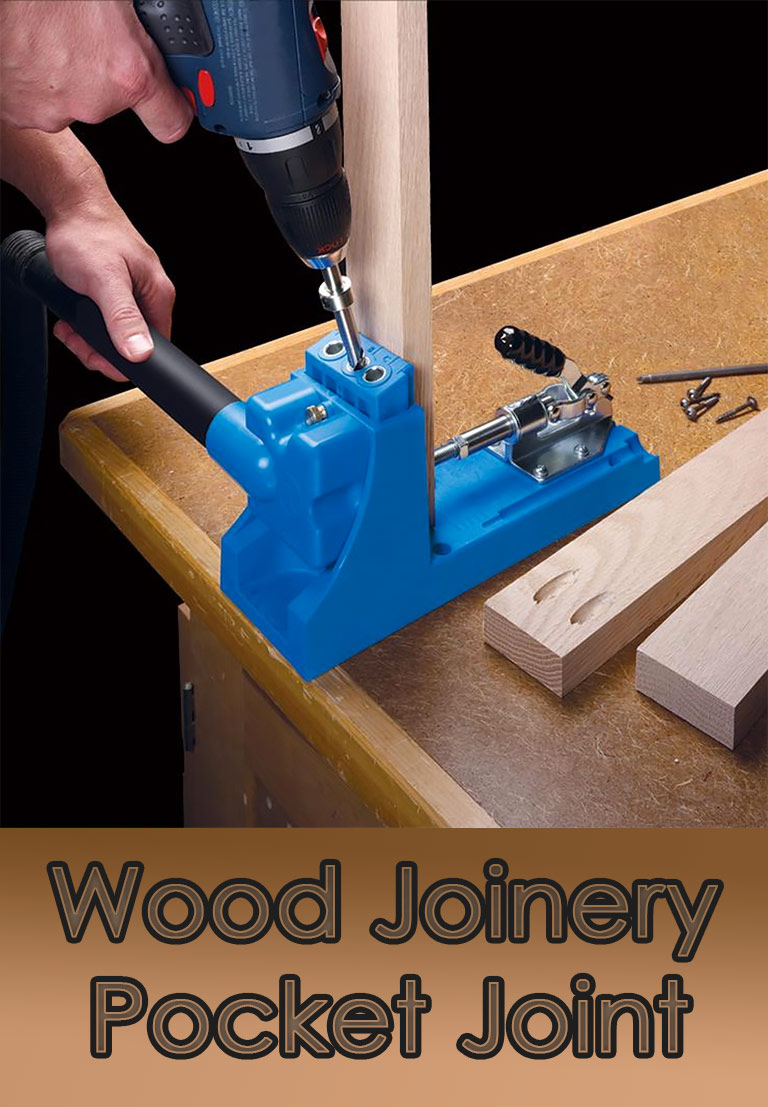
Pocket joints are nothing more than a screw that is driven diagonally through one board into another. Pocket joints are very similar to dowel joints and mortise & tenon joints. To create a proper pocket joint, the path for the screw must be pre-drilled to avoid splitting the head piece. While this can be done by eye, an easier method for drilling consistent pocket joints is to use a pocket-hole jig. The screw is driven through the head board into the tail stock. No glue is necessary, as the screw will hold the joint securely, but glue would definitely add strength to the joint.
Improvements in pocket hole jig technology in recent years have made pocket joints not only easy, but often preferred in certain applications such as many types of face frames. There are numerous different styles of pocket joints, but the basic idea is a jig with a machined aluminum guide cylinder is positioned at a precise angle in the jig. The jig is then clamped to the head board and a special bit the same diameter as the hole (with a much smaller bit on the tip) is used to drill through the aluminum cylinder into the head board.
Once the pocket hole has been drilled in the head board, the tail board is clamped into place and a screw is driven through the pocket hole into the tail board. If glue is to be added to strengthen the joint, it should be placed on the mating surface between the tail board and head board before inserting the screw(s).
Popular Uses for Pocket Joint:
While the most common use for pocket joint is in face frames, there are many other possible applications. Pocket joints can be used to join edges to make a table or cabinet top.
They are also very effective when attaching relatively thick edge banding to plywood or a table top. Pocket joints can even be used to connect angled joints in woodworking projects such as braces for leg rails.
Leave a Reply